Date:
May 17, 21
Today is the introduction of LINE QC SPECIALIST
This system was jointly developed by a talented Japanese engineer and our company.
Quality control software for mass production factories of individual parts.
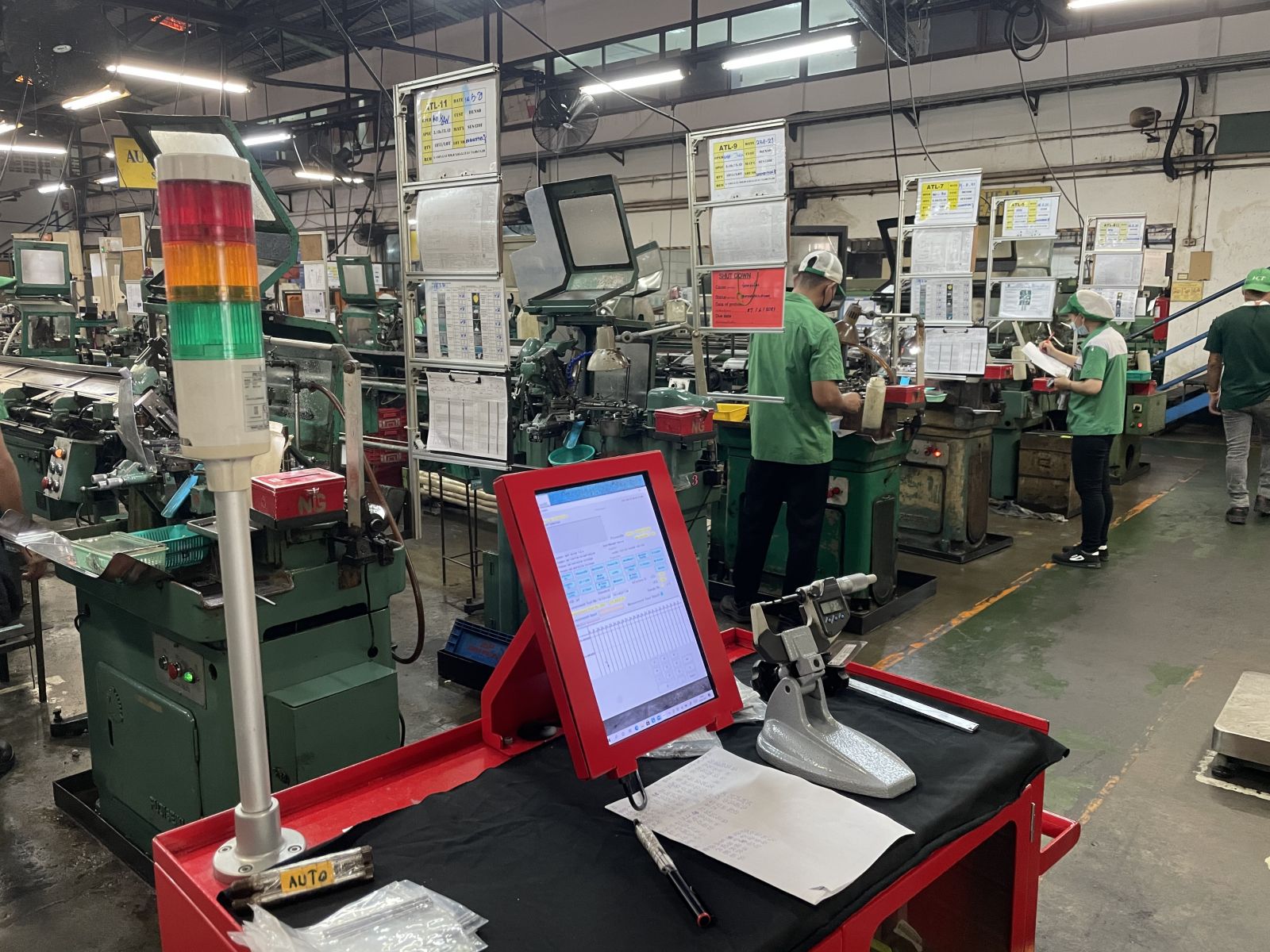
LINE QC SPECIALIST in operation in the process of our camera type automatic lathe
First of all, from the introduction of appearance.
Patrite (green, yellow, red) on tablet,
Comes with Mitutoyo's micrometer and calipers *
It is a mechanism that is automatically transferred by U-WAVE (measurement data wireless communication).
The software is integrated with the wagon so that you can tour the site with it.
It is a device that manages trends while recording data during mass production.
* Other U-WAVE compatible dial gauges can be used.
* Other U-WAVE compatible dial gauges can be used.
Paperless data management is just a secondary function
The biggest feature of this system is that it is a software-integrated device that aims to prevent NG from being created.
Mechanism that does not make NG + "Quality improvement by big data analysis" = LINE QC SPECIALIST.
What does it mean to not make NG?
Specifically, it is studded with a mechanism that allows workers to follow the rules.
As long as you follow the internal rules and manage trends, you should not be able to make defects.
But why do defects occur every day?
In fact, most of the motives for creating the cause are human error that ignores the rules.
Normally, there is no choice but to monitor while improving the level of workers through training.
LINE QC SPECIALIST is a mechanism to avoid this human error in the system.
for example,
・ Calibration of measuring instrument: Thorough calibration work before mass production for each shift
・ Rules for mass production approval process based on three standards (customer specifications> internal control values> central management) Setup, start-up, and mass production start system
・ The timer operates and the system monitors the measurement time to avoid measurement omissions.
If you deviate from these rules, all red lamps will light up.
Of course, even during mass production, as soon as the measured value reaches the control value, the machine will be stopped and adjustment will be urged.
It's just a matter of course, but in fact, I keep doing this as a matter of course.
Everyone should be able to sympathize with the fact that it is extremely difficult to continue on-site.
LINE QC SPECIALIST will take care of this monitoring work on your behalf and the administrator.
Probably not as much as this e-mail newsletter! w
However, in fact, big data collected in units of one month, three months, and six months is a treasure trove in promoting quality improvement.
In particular,
・ You can analyze the process capability of each item and each person in charge.
・ Equipment health examinations (preceding equipment maintenance) can be performed from the process capability of each machine.
・ It is possible to evaluate and monitor people based on the process capability of each worker.
・ Change point management (coolant, blade change, person, machine, material, construction method) is also possible
In the unlikely event that a defect occurs, it will be easier to track down and investigate the cause.
In processes where there is a concern that defects will increase if continuous processing is performed, such as mold and blade wear.
It is a company where central management and trend management function effectively.
From around April this year, we prepared three demo machines and started PR.
Thanks to you, we have already received applications for demo machines from more than 10 companies.
The first team is about to reach the end.
We have received a fair evaluation from customers who are operating the demo machine.
I'm sure it will be useful in your field as well.
If you are interested, please use the demo machine once.
Please experience the mechanism to follow the rules and the effective use of big data in the field.
See you again.
Let's make this week a wonderful week ♪
This system was jointly developed by a talented Japanese engineer and our company.
Quality control software for mass production factories of individual parts.
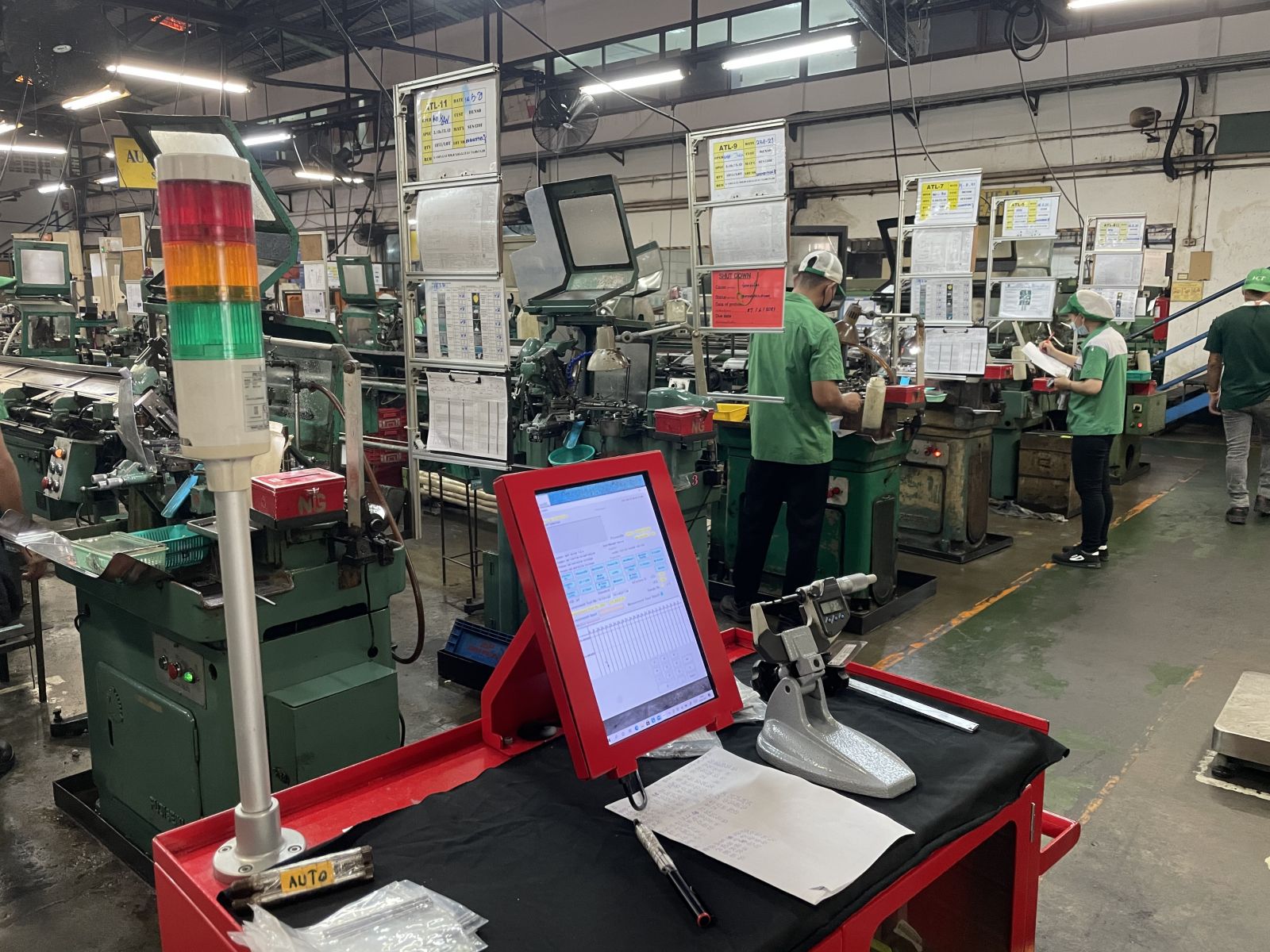
LINE QC SPECIALIST in operation in the process of our camera type automatic lathe
First of all, from the introduction of appearance.
Patrite (green, yellow, red) on tablet,
Comes with Mitutoyo's micrometer and calipers *
It is a mechanism that is automatically transferred by U-WAVE (measurement data wireless communication).
The software is integrated with the wagon so that you can tour the site with it.
It is a device that manages trends while recording data during mass production.
* Other U-WAVE compatible dial gauges can be used.
* Other U-WAVE compatible dial gauges can be used.
Paperless data management is just a secondary function
The biggest feature of this system is that it is a software-integrated device that aims to prevent NG from being created.
Mechanism that does not make NG + "Quality improvement by big data analysis" = LINE QC SPECIALIST.
What does it mean to not make NG?
Specifically, it is studded with a mechanism that allows workers to follow the rules.
In mass production factories, except for sudden troublesFollow the rules
As long as you follow the internal rules and manage trends, you should not be able to make defects.
But why do defects occur every day?
In fact, most of the motives for creating the cause are human error that ignores the rules.
Normally, there is no choice but to monitor while improving the level of workers through training.
LINE QC SPECIALIST is a mechanism to avoid this human error in the system.
for example,
・ Calibration of measuring instrument: Thorough calibration work before mass production for each shift
・ Rules for mass production approval process based on three standards (customer specifications> internal control values> central management) Setup, start-up, and mass production start system
・ The timer operates and the system monitors the measurement time to avoid measurement omissions.
If you deviate from these rules, all red lamps will light up.
Of course, even during mass production, as soon as the measured value reaches the control value, the machine will be stopped and adjustment will be urged.
It's just a matter of course, but in fact, I keep doing this as a matter of course.
Everyone should be able to sympathize with the fact that it is extremely difficult to continue on-site.
LINE QC SPECIALIST will take care of this monitoring work on your behalf and the administrator.
Do you see the inspection data in the process?Quality improvement through data analysis
Probably not as much as this e-mail newsletter! w
However, in fact, big data collected in units of one month, three months, and six months is a treasure trove in promoting quality improvement.
In particular,
・ You can analyze the process capability of each item and each person in charge.
・ Equipment health examinations (preceding equipment maintenance) can be performed from the process capability of each machine.
・ It is possible to evaluate and monitor people based on the process capability of each worker.
・ Change point management (coolant, blade change, person, machine, material, construction method) is also possible
In the unlikely event that a defect occurs, it will be easier to track down and investigate the cause.
It is easy to imagine a cutting factory / forging factory.What kind of company can you use it?
In processes where there is a concern that defects will increase if continuous processing is performed, such as mold and blade wear.
It is a company where central management and trend management function effectively.
From around April this year, we prepared three demo machines and started PR.
Thanks to you, we have already received applications for demo machines from more than 10 companies.
The first team is about to reach the end.
We have received a fair evaluation from customers who are operating the demo machine.
I'm sure it will be useful in your field as well.
If you are interested, please use the demo machine once.
Please experience the mechanism to follow the rules and the effective use of big data in the field.
See you again.
Let's make this week a wonderful week ♪