Date:
September 07, 20
[Thailand / zero defective products] Innovative system ‘LINE QC SPECIALIST’ that does not produce NG (defective) parts in the line process is now fully operational in Thailand! (Part 2)
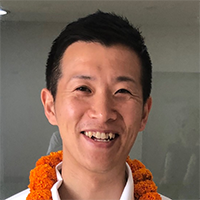
07/09/2020
Q. I don't want to spend too much on capital investment and would like to know how many machines can be managed per MQS (Mobile Quality Station) wagon equipped with the LINE QC SPECIALIST system.
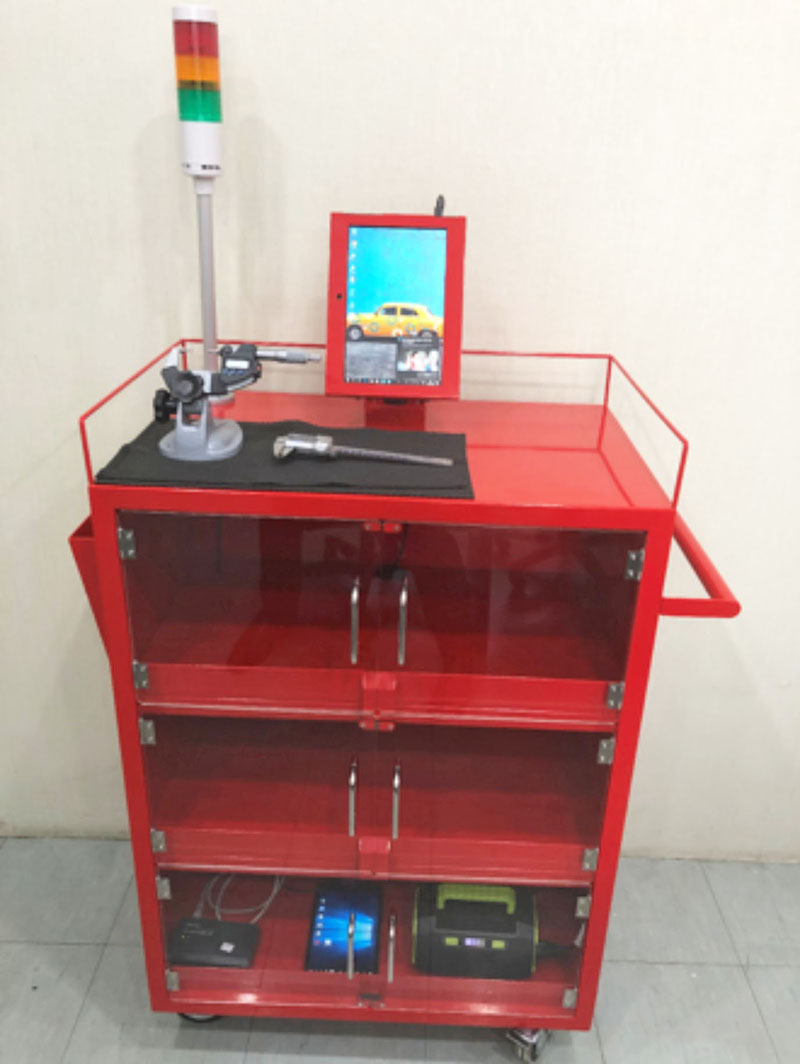
▲MQS Wagon
A. It is possible to manage 7 to 12 machines per wagon, depending on the number of machines you want to manage and the measurement points of the product. We will propose the optimal number of units according to the customer's request.
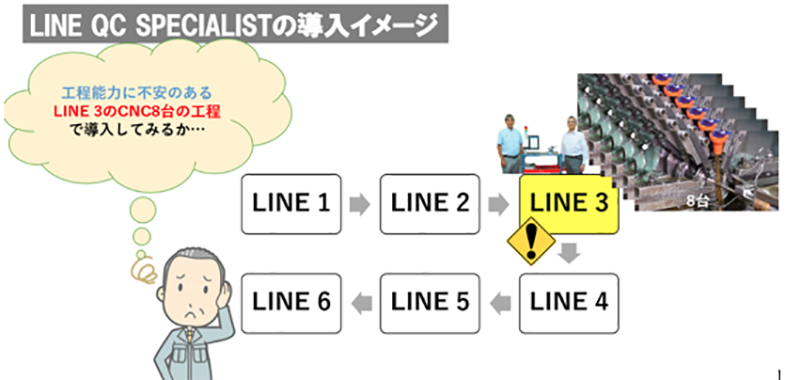
Q. Is it possible to use the system for any product or industry?
A. Yes, basically any company in any industry that manufactures a single product (mass production product) can use it. Currently, we are receiving inquiries mainly from customers related to automobiles, motorcycles, and electric machinery, but it can also be implemented in other industries. The material of the product can be used by companies that handle plastic and rubber products in addition to metal. For more information, please contact us.
Q. How difficult is the terminal operation and how much is the burden on the site?
A. The tablet screen installed on the MQS wagon allows intuitive operation. Since the report after measurement is also automatically performed, it is possible to avoid entry errors and save labor, and it is possible to be operated correctly even by new staff and those with little manufacturing knowledge.
Q. What should I do if I want to learn more or want to consider Line QC Specialist further?
A. A. First of all, please feel free to contact Oishi/Yada at our company. We can visit your company or have an online video meeting remotely. If you can come to our factory, we can show you how it actually operates in the factory. I think it's easier for you to imagine how the system can be implemented and used.
We are also looking for LINE QC SPECIALIST monitor companies. This is a trial campaign where you can participate in the monitor with the minimum amount of a deposit, try the introduction and experience, and if there is no prospect of implementation, the deposit is refunded.
LINE QC SPECIALIST is committed to quality improvement!
In manufacturing, quality control is like a diet.
1. Weigh and record fluctuations every day
2. Record what you ate and its calories every day
3. Record calories burned using a pedometer every day
Visualization ⇒ Consciousness ⇒ Change behavior ⇒ Lead to results
In this way, visualize daily changes and consciously reduce the amount of food, exercise, and make efforts. Doing so will lead to results. In the sense that quality control also grasps the capabilities of the current factory and bridges the gap between ideal and reality, I think that steady efforts similar to dieting are required.
Up to now, even though quality control can be done in an outlook by procedures such as creating a manual, the actual operation at the site is often not reliable... It may be said that "LINE QC SPECIALIST is like a strict diet program!". We would like our customers to use our system to commit to improving quality, and we would like to work with our customers to “Eliminate in-process defects.”